Energy Efficient: Saving Staff Time and Effort
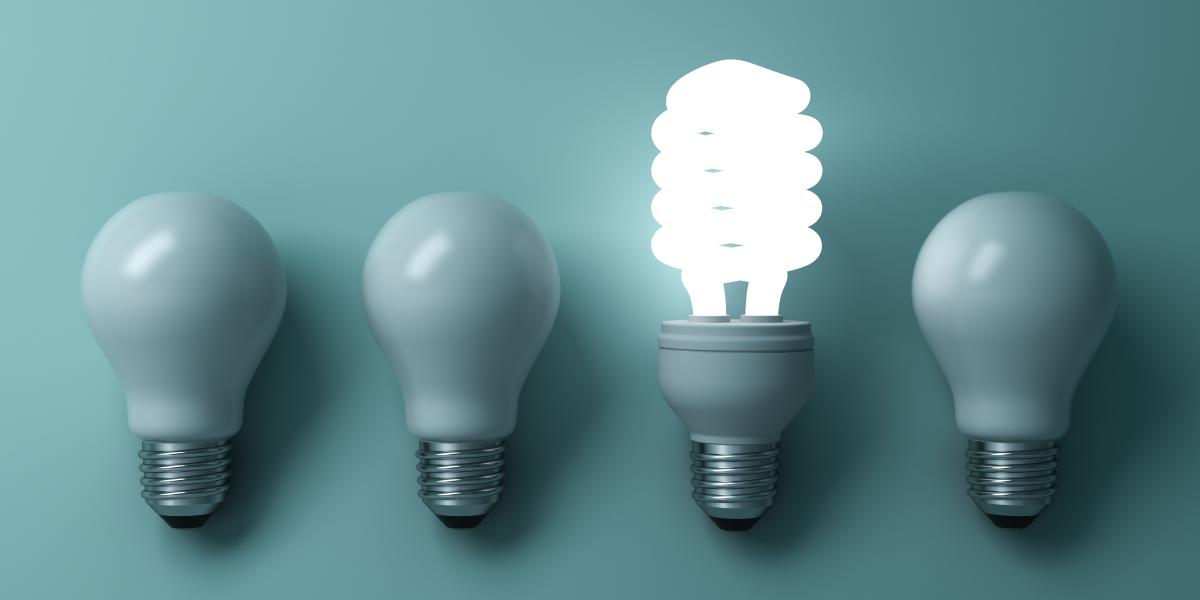
While higher education has not historically had to focus on efficiency, recent budget cuts and enrollment pressures increasingly require colleges and universities to streamline their operations. Applying certain aspects of the corporate world to international education can help institutions use their best resource—staff members and their time and efforts—more efficiently, says David Di Maria, EdD, associate vice provost for international education at the University of Maryland-Baltimore County (UMBC).
Drawing on principles from industries such as manufacturing and healthcare, lean processing is a management approach that improves efficiency. “Lean process improvement is about increasing value while eliminating wastes,” says Di Maria, the author of a forthcoming NAFSA book about using lean process principles in international education, Achieving More with Less: Lean Management in the International Student Office. For example, hospitals identify how to shepherd patients more quickly through emergency rooms while improving the quality of care, and factories look for ways to move products more efficiently along the assembly line.
In an international office, this might look like prospective student applications being reviewed more efficiently, allowing institutions to evaluate more applications and respond to applicants in a timely manner. Applying aspects of lean processing can help international educators during a time when more is being asked of them—and, in many cases, with fewer resources than ever.
Doing More with Less
Di Maria has used a lean management approach in the international offices at several institutions. While completing a management certificate program 10 years ago, he realized how manufacturing principles might be